Turning waste into wealth: the future of manufacturing with waste feedstock
Local microfactories have the potential to sustainably supply the metals and critical materials needed for Australia’s green transition. But what are the right policy settings to support the reprocessing of waste for manufacturing?
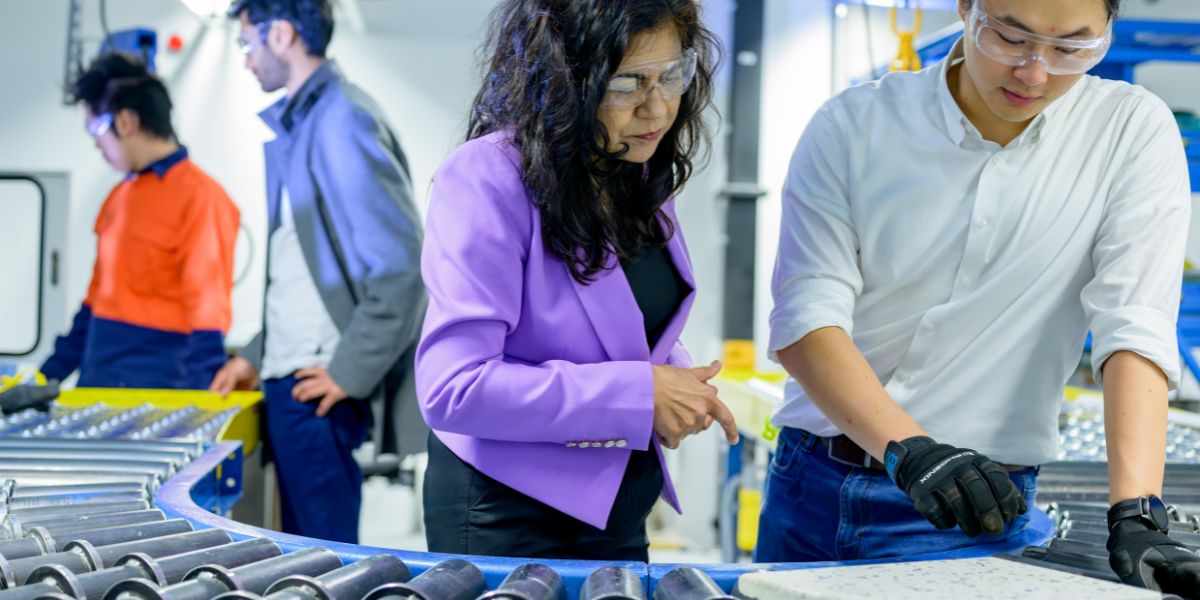
20 August 2024
Sustainability is no longer a choice – it’s a necessity. The transformation of waste into valuable feedstock for manufacturing represents a profound shift – and opportunity – in our approach to resource sustainability and decarbonisation.
This paradigm shift is particularly crucial for the metals and critical materials needed for future electrification, such as batteries and renewable energy infrastructure. As we transition to a more electrified world, the demand for these materials will skyrocket.
But missing from the renewable energy discussions is the vital ingredient of “using waste as a resource” to secure national capability and capacity for future green metals and energy production. When considering true sustainability and the creation of a circular economy, the role of waste must be central to those efforts.
Addressing this demand sustainably requires innovation, including the integration of waste feedstock into the manufacturing process and the rise of microfactory technologies for decentralised and localised production, particularly where waste resources are located.
Indeed, the alignment of recycling and manufacturing of metals can readily shift the sustainability dial for Australia. With BHP closing its Australian nickel operations and foreshadowing future copper mine closures, finding new ways to source the vital materials needed for sovereign capability and renewable energy infrastructure is now even more urgent.
We must strive for a circular economy – or many localised circular economies – in which materials are kept in use for as long as possible via new decentralised green manufacturing technologies, and then use these recovered materials to establish new business supply chains.
Some emerging technologies are available to reform valuable materials contained in many of the “hard to recycle” waste types that are not subject to traditional waste and recycling processes. These waste types include: electronic waste (e-waste), battery and PV wastes, as well as recovering metals and polymers from millions of tyres, mattresses, appliances and auto waste.
Waste as a feedstock: a sustainable solution
The global push towards renewable energy and electrification hinges on the availability of metals and other critical materials like lithium, cobalt, nickel and rare earth elements. These materials are essential components of batteries, solar panels, wind turbines, and other clean energy technologies. However, traditional mining and processing of these materials are fraught with environmental challenges, including habitat destruction, water pollution and significant carbon emissions. Moreover, geopolitical tensions and resource nationalism can lead to supply chain vulnerabilities, threatening the stability of the renewable energy sector.
Utilising waste as a feedstock offers a promising solution to these challenges. E-waste, for example, contains significant quantities of precious and critical metals. According to the Global E-waste Monitor 2020, approximately 53.6 million metric tons of e-waste were generated globally in 2019, with only 17.4 per cent officially documented as being recycled. The vast majority of e-waste ends up in landfills, where it poses serious environmental hazards due to the leaching of toxic substances.
By developing efficient methods to recover and recycle these materials from waste, we can reduce the need for virgin resource extraction, mitigate environmental impact and create a more secure and resilient supply chain.
Advanced recycling technologies, such as our UNSW SMaRT Centre technologies, as well as others including hydrometallurgy and pyrometallurgy, can be employed to extract metals from e-waste, while newer, greener methods like bioleaching use microorganisms to recover metals in a more environmentally friendly manner.
The role of microfactories in decentralised manufacturing
Microfactories represent a key innovation in the move towards using waste as feedstock. The World Economic Forum has long lauded the concept, developed by the SMaRT Centre over a decade ago, which has also been recommended in an Australian Parliamentary inquiry into creating a circular economy.
These small-scale, high-tech production facilities are designed to operate with flexibility and efficiency, enabling localised and decentralised manufacturing. By bringing production closer to the source of waste, microfactories reduce transportation costs and emissions, foster local job creation and enhance community resilience.
Decentralising the supply chain for reforming waste materials offers a promising solution to the complex challenges of logistics and material science in recovering critical resources. By allowing a diverse range of organisations to participate, this approach fosters collaboration and empowers entities at various skill levels to take ownership of the process. It is a step towards making the recovery of critical materials from waste resources more accessible and efficient, ultimately benefiting communities.
Microfactories can be particularly effective in the recycling and repurposing of waste materials. For example, a microfactory might be equipped with advanced technologies such as 3D printing, robotics, and AI-driven sorting systems to efficiently process and recycle e-waste. These facilities can disassemble electronic devices, extract valuable metals, and then use those materials to manufacture new products, all within a compact and efficient space.
Microfactories hold various advantages over conventional manufacturing, including:
- Local resource utilisation: Microfactories enable the processing of locally sourced waste, reducing reliance on global supply chains.
- Reduced environmental impact: By localising the recycling and manufacturing process, microfactories significantly cut down on the carbon footprint associated with transporting raw materials and finished products.
- Economic benefits: Establishing microfactories creates local jobs and supports the local economy. It also reduces the costs associated with waste management and material transportation.
- Enhanced innovation: The decentralised nature of microfactories fosters innovation. With the flexibility to adapt quickly to new technologies and processes, microfactories can continuously improve their methods for recycling and manufacturing, leading to greater efficiencies and new product development.
- Community resilience: Localised manufacturing creates a circular economy where waste is continuously repurposed. This reduces the community's dependency on external resources.
The path forward
To fully realise the potential of waste as a feedstock resource and the role of microfactories in this transformation, several key actions are needed.
First, governments and private sector entities should invest in the development of advanced recycling technologies and the establishment of microfactories. This includes funding research and development, as well as creating incentives for businesses to adopt these technologies.
Second, policymakers need to create a favourable regulatory environment that supports the use of waste as feedstock and the establishment of microfactories. This could include tax incentives, grants, and streamlined permitting processes.
Third, raising public awareness about the benefits of recycling and the potential of microfactories. Educational campaigns can help communities understand the value of waste and encourage participation in local recycling programs.
And finally, collaboration between governments, researchers in academia and the private sector is crucial for the successful implementation of waste-to-resource initiatives. Partnerships can facilitate knowledge sharing, technological innovation and the scaling of successful models.
A unique opportunity now exists in Australia to integrate waste as a resource for future manufacturing needs through the Commonwealth Government’s Future Made in Australia agenda which aims to foster significant private sector investment for priority industries.
The two major streams that government funding will support in the coming years – net zero and economic security – are the right vehicles for developing circular economies.
To drive this agenda forward, a framework of criteria is needed that includes both principles and standards around the use of recycled feedstock, the implementation of lifecycle assessments to ensure sustainable use of materials, and enforcement through product stewardship and procurement rules.
Our Sustainable Communities and Waste Hub at the UNSW SMaRT Centre is leading alongside other partners under the National Environmental Science Program to provide policy suggestions and initiatives to help build the momentum in this direction.
Importantly, the focus on delivering capabilities such as decentralised waste-to-product technologies must be a priority for remote and regional locations where waste stockpiles can be transformed into the feedstock needed for future manufacturing.
The shift towards using waste as a feedstock for manufacturing is not just an environmental imperative but also an economic opportunity.
By harnessing the power of microfactories, we can create a decentralised and resilient manufacturing ecosystem that reduces waste, conserves natural resources and supports local economies.
Professor Veena Sahajwalla is an internationally recognised materials scientist, engineer, and inventor revolutionising recycling science. She is renowned for pioneering the high temperature transformation of waste in the production of a new generation of “green materials” at the UNSW Sustainable Materials Research and Technology (SMaRT) Centre, where she is Founding Director. Veena is the inventor of polymer injection technology, known as green steel, an eco-friendly process for using recycled tyres in steel production. In 2018, Veena launched the world's first e-waste MICROfactorieTM and in 2019 she launched her plastics and Green Ceramics MICROfactoriesTM, a recycling technology breakthrough. She is also the director of the ARC Industrial Transformation Research Hub for ‘microrecycling’, a leading national research centre that works in collaboration with industry to ensure new recycling science is translated into real world environmental and economic benefits. In 2021, Veena featured in the ABC’s Australian Story and she was named the 2022 NSW Australian of the Year in recognition of her work.
Anirban Ghose is Head of MICROfactorieTM Technologies at the UNSW SMaRT Centre. Combining his mechatronics, nanoscience and engineering backgrounds, Anirban has in depth research and practical experience of recycling material opportunities, and the identification and development of technologies for incorporating recycled materials and goods into useable products. Working at the forefront of recycled materials innovation, he leads a team of engineers and takes a lead role in stakeholder management, including industry partners, working closely with Professor Sahajwalla. In 2023, Engineers Australia awarded him the Emerging Professional of the Year Award NSW.
Image credit: UNSW SMaRT Centre
Features
Michelle O’Shea, Nicola Street & Daniell Howe
Sue Kleve, Katherine Kent and Rebecca Lindberg
Subscribe to The Policymaker
Explore more articles
Jack Wilson, Kate Ross and Steph Kershaw
Tom Longden and Gina Gatarin
Features
Michelle O’Shea, Nicola Street & Daniell Howe
Sue Kleve, Katherine Kent and Rebecca Lindberg
Explore more articles
Jack Wilson, Kate Ross and Steph Kershaw
Tom Longden and Gina Gatarin
Subscribe to The Policymaker